DIY Silicon: Man Builds Integrated Circuit That's Similar to Intel's 4004 CPU
Table of Content
This means that a silicon chip made with a silicon wafer would cost around two hundred dollars. It would have to be fabricated in a factory, which takes time and patience. A fabricated chip would be made using a silicon wafer. If a silicon wafer chip costs more than two hundred dollars, it is more expensive to build. The packaging of the dies includes a substrate and a heat spreader, and they take on the recognizable shape of a desktop CPU. Heat is transferred from the silicon by the heat spreader into the heatsink positioned on top of it.
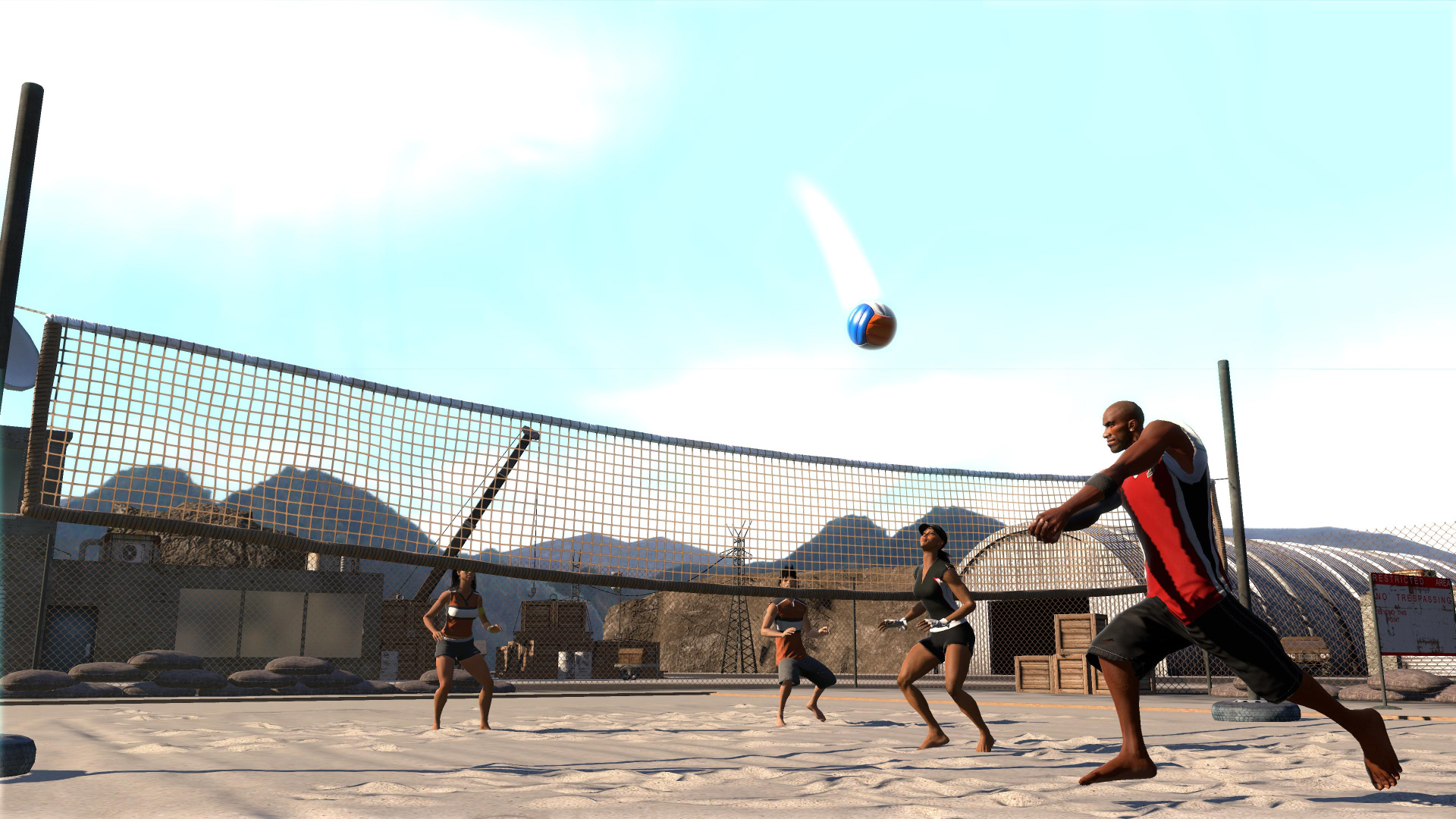
But nonetheless, a great future awaits him if he can keep learning at this rate. Now in 2021 Zeloof has created his second computer, chip called the Z2. This chip is orders of magnitude greater than the Z1, with 1200 transistors on a single chip compared to just six on the Z1. First you need a mask, create a design in photoshop/paint and then from staples have 2 copies made of it. You need it double layered to fully block out the light in certain areas.
How to Make a Computer Chip at Home
During this process, the etched silicon is then exposed to a photoresist and subsequently baked again. The next step in the process is to develop the photoresist. If you thought building homemade computer chips was impossible, you would be wrong. Sam Zeloof has just made his second homemade silicon integrated circuit featuring 1200 transistors, by using the same techniques as Intel did with its first CPUs in the 1970s. Under some conditions, it conducts electricity; under others, it acts as an insulator. Silicon's electrical properties can be altered by the addition of impurities, a process called doping.

Chip manufacturers first cut silicon wafers to the desired size to make a computer chip. The wafers are then polished and cleaned before any further processing can take place. Once they are cut, they undergo a series of processes that add layers of different materials to the surface of the die. These layers serve different purposes, such as creating electrical paths or isolating different regions of the chip.
Step 2: Purify to Obtain Silicon Ingot
Along with that we need a few small computer fans to blow the air through the filters. If an animal gets lost, the workers at animal shelters can scan the animal for the chip, which can provide contact information for the owner. In the event that your pet gets lost, they will not only be able to be identified, but also find out where the owner is, thereby saving their lives. This technology is incredibly helpful, but there are some things you should know before investing in one. Engineers than use the photolithography process to create the chip architecture.
For comparison, Intel's 4004 CPU had 2200 transistors, while the Z2 has 1200 and is built on the same process. What took a whole company to do in the 1970s is now being done by a single person in his own home. Silicon is a gray color that changes with the amount of oxide grown.
How Are Computer Chips Made?
What you should end up having then is a flap on the inside of your container where you can open and close it as a door to your cleanroom. What is the difference between a silicon wafer CPU and an ordinary chip? The silicon nitride-based semiconductor is much cooler to operate and uses less power than the standard chip. However, the size and weight of a silicon wafer make the CPU much larger than the usual chip. The wafer requires a lot of power to operate properly, which has to be brought in through the silicon wafer and voltage regulators. Typical silicon wafer used in an integrated circuit before the substrate is removed from it's wafer carrier.
Unexposed areas are then etched away by hot gasses to reveal the silicon dioxide base below. The base and the silicon layer below are further etched to varying depths. There are few things in the world as simple as sand, and perhaps none as complex as computer chips. Microchips are created by layering interconnected patterns on a silicon wafer. From design to mass production, the microchip manufacturing process contains hundreds of processes and can take up to four months. A thin silicon layer is removed from the surface by applying reactive chemicals.
Step 2: Oxide Growth and Diffusion
Note though even with the clear film it does dim down the laser light a bit ~30%. The photolithography processes is repeated almost 50 time before the the chip is ready to be packaged and shipped. Wire cutting into individual slices damages the wafer. Several more procedures are then used to smooth the silicon surface to a flatness that can be used in Integrated Circuits . The silicon crystal weight depends on the diameter of the ingot. For example a 200mm silicon crystal ingot is about 440 pounds.
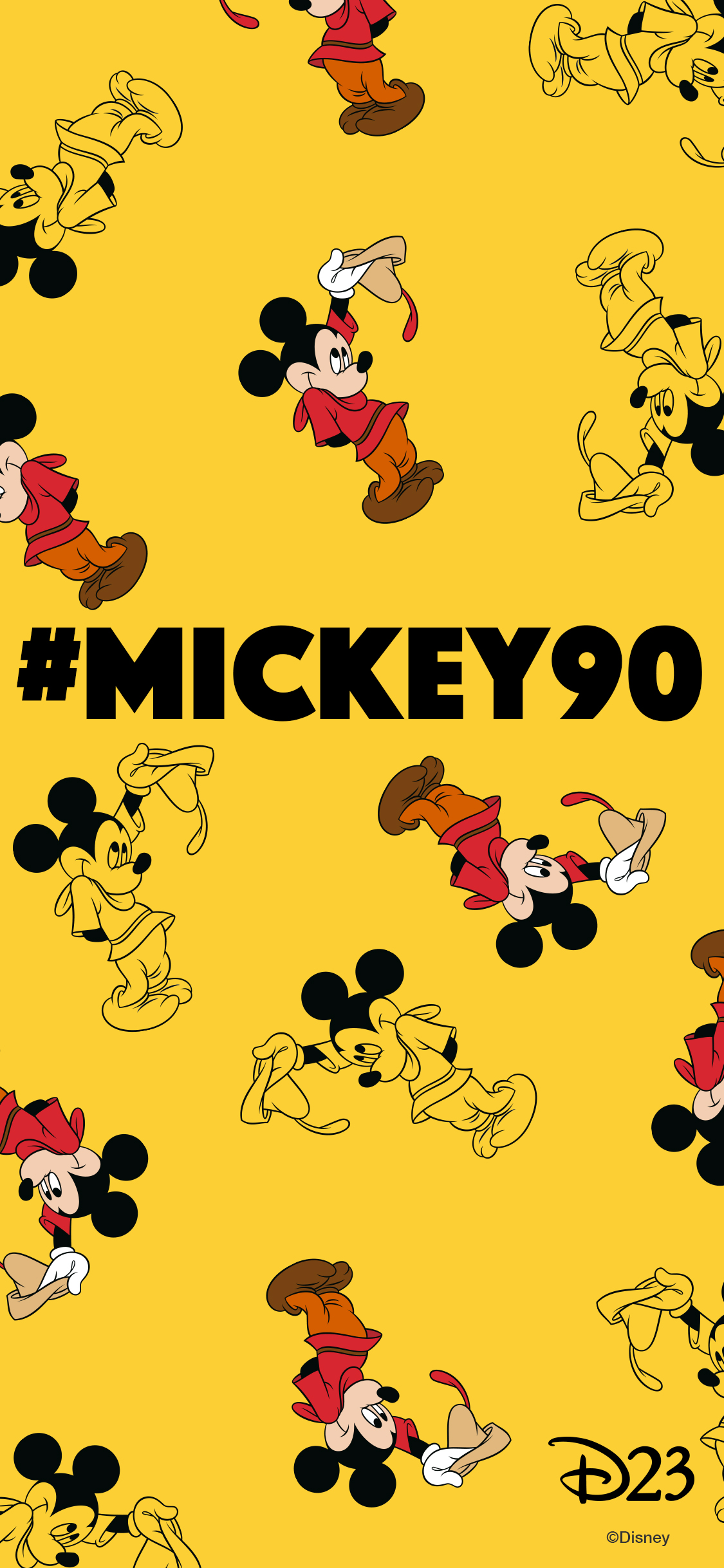
These are applied at different rates depending on how deep you want them to go into the surface. If you want to remove a large amount of material, apply the chemicals for longer periods so that they can be as strong as possible. By repeatedly etching and re-imaging this way, engineers can create complex patterns for different components like memory chips and processors. The silicon nitride cpu is a silicon wafer that is based on a silicon wafer. These chips are made of a single silicon nitride, and have multiple transistors. One wafer can contain up to three million components.
Sometimes several layers of conductors, separated by glass insulators, are laid down. Doping is the process of bombarding the silicon wafer with ions to change its conductivity once the exposed photoresist has been wiped off. After washing off the leftover photoresist, a pattern of impacted and unaffected material is revealed. Following that cut an opening on the side for a hepa filter and fan, then silicone/hot glue them in.
Silicon wafers are the building blocks of computer chips and are an essential part of many modern devices. They are polished and refined before being exposed to a process known as photolithography. The silicon is covered with a layer of photoresist material and is exposed to a UV light mask in order to create the pattern of microprocessor circuits. During this process, the photoresist layer becomes soluble and is washed away by a solvent. The exposed photoresist is then stamped onto the silicon wafer with a hard material.
A large silicon crystal, which may weigh several hundred pounds, is then cut in thin slices called wafers. After a silicon wafer is cut, the material is buffered to remove impurities. A silicon wafer is made by spinning molten silicon in a crucible. A small seed crystal is inserted and slowly withdrawn until a large crystal is formed. Upon completion, a large, solid silicon wafer weighing several hundred pounds is produced. Then, it is cut into thin slices called wafers and buffered to remove impurities.
Comments
Post a Comment